Help us redesign our market leading live-cell research product, Incucyte. Students on the Sartorius team will provide the initial conceptual design and prototype work to develop a new, miniaturized, precision Live-cell Research Platform.
“Instead of placing our microscope inside and incubator,
Can we put the incubator inside the microscope?”
Abstract:
The Incucyte product is a research tool that allows scientists to observe experimental progress and perform real-time, live-cell imaging over long periods without disturbing cell development. Sustaining live cell cultures requires incredibly tight control of the environment over long periods of time (e.g., even tiny changes in temperature (0.2 C) could destroy an experiment). Other parameters, such as relative humidity, CO2 levels, airflow rates, etc. have similarly tight requirements.
The status quo design solution places the Incucyte tray within a large incubator designed to keep the cells in a stationary and controlled environment. This design has proven commercially popular amongst biologists. One of the challenges of this design is that it forces all parts of the equipment to fit within the space available in the incubator, thus limiting and complicating additions of functionality.
Students on this project will complete the initial technical design and feasibility study and construct a phase I prototype of the next generation of live-cell equipment, consisting of a much smaller incubator, able to hold the Incucyte tray and externalizing all other subsystems (imaging, temperature control, humidity control, etc.). The challenge of the project will be to achieve size reduction while maintaining the necessary precision performance of the unit.
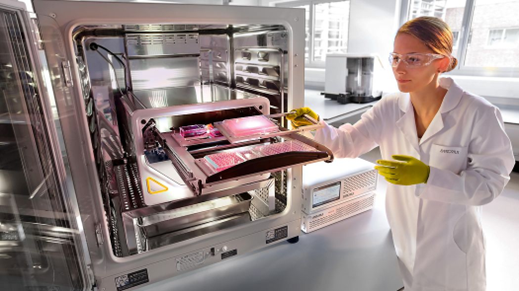
Impact:
This project will provide the basis for a whole new line of live-cell research products, accelerating the pace of scientific discovery, and improving Sartorius’ position in the marketplace.
Scope:
Minimum Viable Product Deliverable (Minimum level of success)
- Complete literature review of cell culture incubators and microscope stage incubators, including academic literature, benchmarking, patents, and Sartorius expert knowledge.
- Determine a list of technical requirements (these can leverage the existing product)
- Supported by the mentors, select a suite of high-precision test sensors and controllers. Develop control structures capable of delivering precision necessary.
- Complete an initial modeling exercise to estimate the smallest possible unit that could deliver the controlled environment necessary. Decide on the dimensions and construction of the phase I test system. Consider function and cost of insulating materials.
- Design and build a phase I prototype that that supports a standard Incucyte tray, provides transparent access for image equipment, and can be used to demonstrate precision temperature control.
- Tune the control system and evaluate the performance of the phase I prototype against the requirements of the project, demonstrate extended precision control, and develop a strategic plan for revising the prototype.
Expected Final Deliverable (Expected level of success)
- Revise the prototype design and build a phase II prototype.
- Implement design improvements to deliver controlled parameters in at least one other variable.
- Using current imaging subsystems, demonstrate that imaging can be successfully performed through whatever transparent solution the team develops.
- Provide data logging of sensors and system status, ideally connected to a simple web U/I.
Stretch Goal Opportunities: (High level of success)
- Complete precision control demonstration of all environmental parameters on an extended validation test over multiple weeks.
- Add functionality to allow for bright-field and epifluorescence imaging of microplates within the incubator.
- Work with the Sartorius biology team to test the design with live cells!
Hardware and Sensor Integration (2-3 Students)
Specific Skills: Control system development, circuit design, sensor selection, evaluation, integration, and sensor design.
Completion of EECS 460 and or EECS 461 is a plus.
Likely Majors: EE, CE, ECE, ROB, ME
Heat Transfer and Fluids Modeling (1 Student)
Specific Skills: Intermediate heat transfer and fluids modeling.
Likely Majors: ChE, ME, MSE, AERO
Mechanical Design and Systems Engineering (2-3 Students)
Specific Skills: Determining user needs, experimental design, testing and evaluation, integrating mechanical and electrical components, modeling heat transfer and other environmental variables
EECS 314 or equivalent is a strong plus
Likely Majors: ME, BME, ROB
Additional Desired Skills/Knowledge/Experience
Strong candidates will have familiarity or experience with some of the following items, and a positive attitude to learn what is necessary, as the project gets underway.
If you have any of these characteristics, highlight them on your Experience and Interest Form and talk about them in your (optional) one way video interview.
- Passion for the field of biotechnology
- Interest in developing control systems
- Hands-on, proactive approach to work
- Successful team-based experience in any context
- Practical mechanical system design skills: 3D printing, Sensor/hardware integration, basic controls, fast prototyping, CAD, machining, etc.
- Experience with Arduino, Raspberry PI, or similar
- Biolab experience, particularly live cell experience
Sponsor Mentor
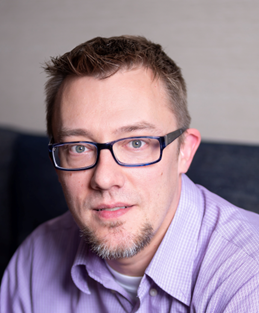
John York
John is a UM computer engineering alumnus. John has supported several MDP projects in the past, mostly for software and machine learning. John has experience working with small startups as well as large global companies, both as a leader within the technology and product management teams.
Executive Mentor
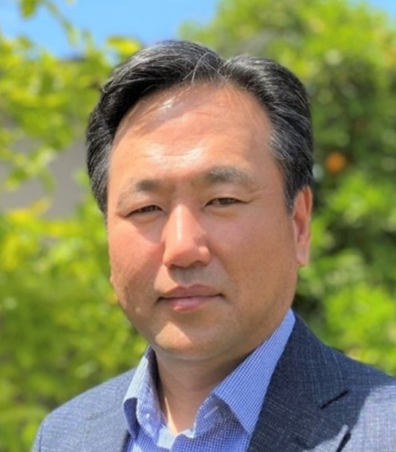
Tae Kang
Tae has been a part of the life science industry since 1999, holding roles as both an engineer and manager in various roles. He has contributed to the development of various life science microplate readers and instruments. Currently, Tae manages the engineering team for the Lab Products and Services division in North America.
Faculty Mentor
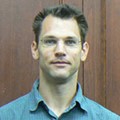
Peter Seiler
Associate Professor, Electrical Engineering and Computer Science
Peter works in the area of robust control theory, which focuses on the impact of model uncertainty on systems design. He is a co-author of the Robust Control Toolbox in Matlab. He is currently developing theoretical and numerical algorithms to assess the robustness of systems on finite time horizons. He is also investigating the use of robust control techniques to better understand optimization algorithms and model-free reinforcement learning methods. He joined Michigan in 2020 from the University of Minnesota, where he had been working on advanced control techniques for wind turbines, fault-detection methods for safety-critical systems, and robust control of disk drives. He has a Ph.D. in Mechanical Engineering / Controls from U.C. Berkeley and BSE in Mechanical Engineering / Mathematics from University of Illinois at Urbana-Champaign.
Weekly Meetings: During the winter 2025 semester, the Sartorius team will meet on North Campus on Fridays from 9:00 – 11:00 AM in 4122 EECS.
Work Location: Most of the work will take place on North campus in Ann Arbor, with opportunities to travel to Sartorius’ Ann Arbor office to access labs and equipment and for occasional meetings and presentations with stakeholders. MDP will provide transportation.
Course Substitutions: CE MDE, ChE Elective, EE MDE, CoE Honors, MECHENG 450, MECHENG 490, SI Elective/Cognate
Citizenship Requirements: This project is open to all students. Note: International students on an F-1 visa will be required to declare part time CPT during Winter 2025 and Fall 2025 terms.
IP/NDA: Students will sign IP/NDA documents that are unique to Sartorius.
Summer Project Activities: Students with the right to work in the USA indefinitely without sponsorship will be guaranteed an interview for a 2025 internship. The interviews will take place before the end of March of 2025.
Learn more about the expectations for this type of MDP project