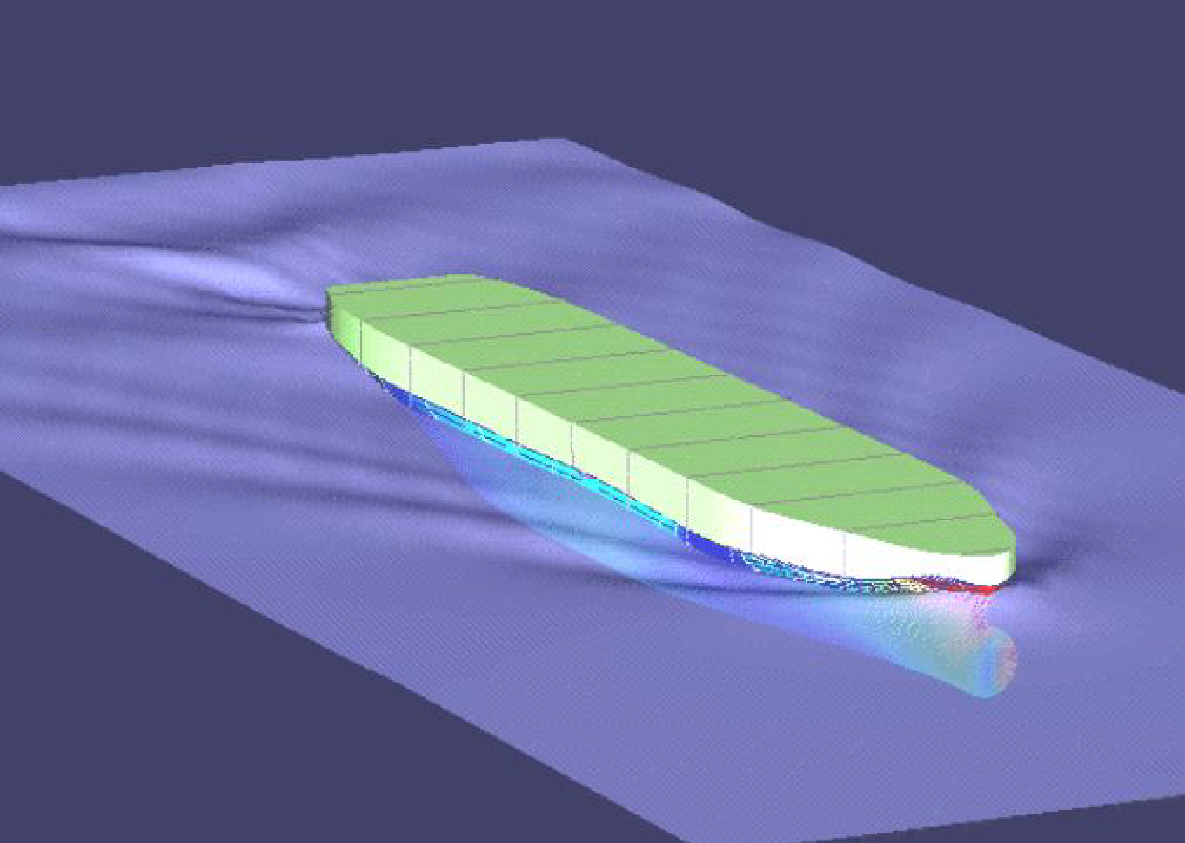

- More efficient vessels are required by the International Maritime Organization (IMO) to meet its ambitious goal to reduce up to 50% the Green House Gas (GHG) emissions from international shipping by 2050.
- A more fuel-efficient ship will be faster and have an increased range without increasing their emissions. This will potentially reduce the costs of goods being transported and improve the reliability of the global supply chain.
- Complete literature/background review that includes basic understanding of hull hydrodynamics and drag reductions strategies, expected ocean freight conditions (speed, loaded weight, conditions), relevant patents, similar solutions from other applications, etc.
- Develop a set of requirements for the design solution.
- Select a representative set of benchmark use cases (different bow shapes, materials, speed, weight of ship, etc.) and determine levels of drag for each.
- Leverage the multidisciplinary background of the team to develop a multitude (50-100) of design ideas to achieve a reconfigurable bulbous bow.
- Evaluate the top design ideas against the expected ability to meet requirements and feasibility for prototyping (access to necessary knowledge and information, materials, fabrication facilities, etc.). This will likely require “mini-project” investigations.
- Guided by the mentors, select one solution concept, and develop a rough prototype.
- Numerical simulations of the drag at different conditions, speeds, and a minimum of 2 bow designs/settings. Estimate the fuel consumption and the efficiency of a ship with a reconfigurable bulbous bow.
- A finite element or CAD kinematic model of the primary solution concept (whichever method is most applicable).
- Tow tank-estimated drag on functional scale model(s) of bow configurations.
- Evaluate the drag results of the testing/modeling and refine the prototype.
- Additional/infinitely adjustable configurations.
- Build prototype that both adjusts and can be tested in tow tank.
Hydrodynamics (2-3 Student)
Specific Skills: Resistance, maneuvering, and performance of platforms and vessels in a marine environment. Likely Majors: NAME, AEROMechanical Design and Prototyping (2-3 Students)
Specific Skills: Design concept generation, determining user needs and techniques for fast prototyping, mechanical structures, and evaluation techniques. Manufacturing skills/ knowledge would be a plus. Likely Majors: NERS, ME, ChE, AEROMechatronics (1-2 Students)
Specific Skills: Mechatronics, controls, system integration, CAD, fabrication. Likely Majors: ME, CE, EEAdditional Desired Skills/Knowledge/Experience
If you have any of these characteristics, highlight them on your Experience and Interest Form and talk about them in your (optional) one way video interview.
- Interest in ships and marine engineering
- General programming/Arduino
- Good fabrication skills
- Mechanical aptitude and spatial relations
- CFD (Computational Fluid Dynamics) software knowledge is a plus
- Experience in coding (Matlab, Python, C++ etc.)
- Proactive, self-motivated individuals with strong problem-solving skills
- Teamwork experience and objective driven attitude
- Communication skills and initiative to communicate
Sponsor Mentor
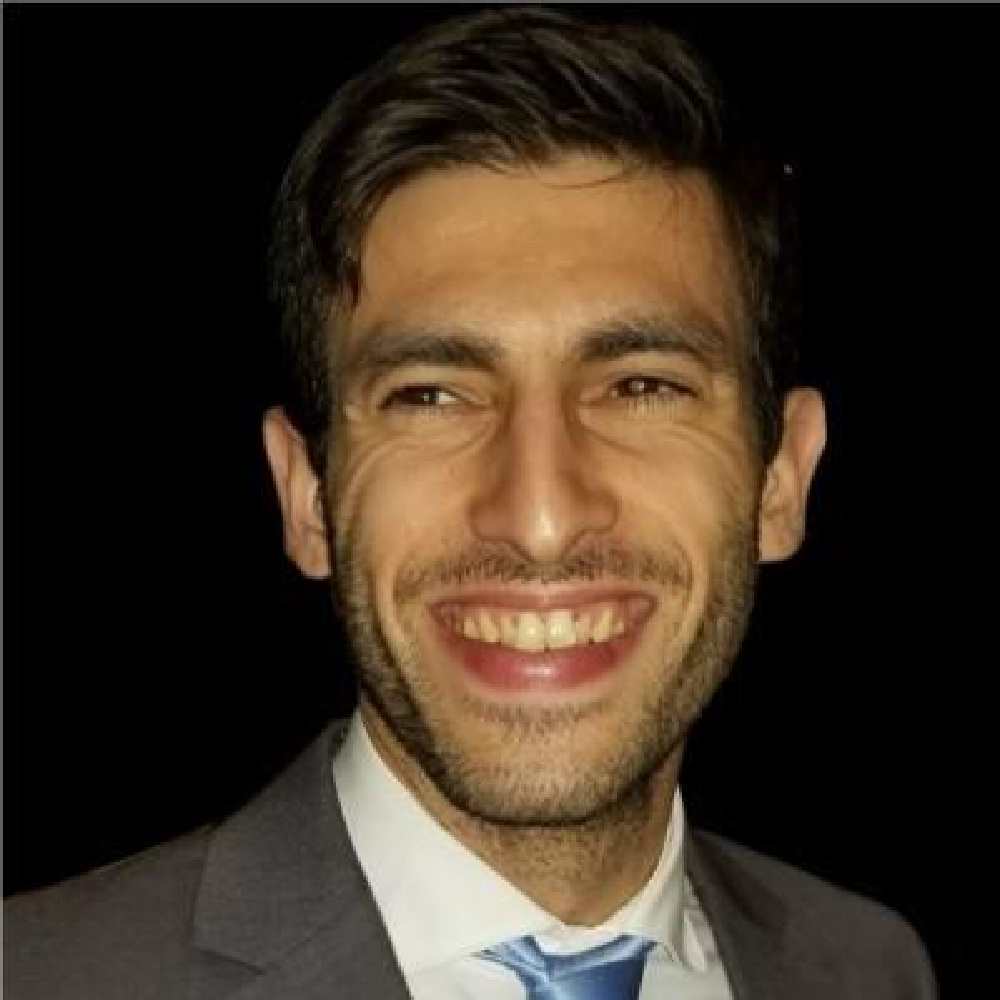
Gabriele Librandi, PhD
Manager for University and Research
Gabriele Librandi, PhD is Manager for University and Research in Fincantieri Marinette Marine in Washington D.C. He oversees research and innovation to expand the company’s capabilities and support its innovative effort. Gabriele holds a Master of Science in Aeronautical Engineering from Sapienza University of Rome, a second Master of Science in Mechanical Engineering from New York University and a PhD at Harvard University in Materials Science and Mechanical Engineering. His prior engineering experience includes Rolls-Royce (UK) GE Global Research, and NASA JPL.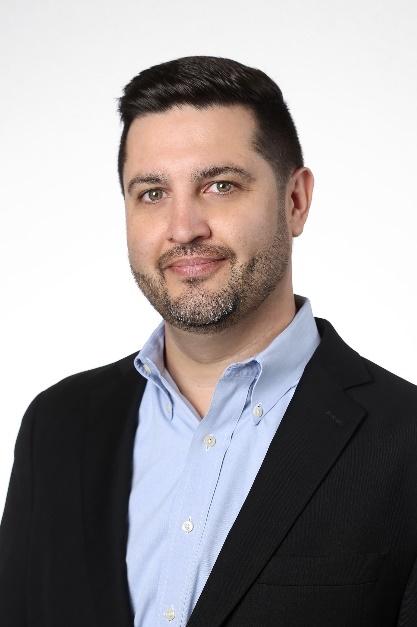
Ross Kanzleiter
Chief Operations Officer
Ross Kanzleiter is the Chief Operations Officer at Fincantieri Marinette Marine (FMM). Ross earned a Bachelors of Science in marine engineering systems from the United States Merchant Marine Academy where he served as the valedictorian of his class, and a Masters of Science in environmental process engineering from Johns Hopkins University. Additionally, Ross has performed further post graduate studies at Purdue University focusing on technology, leadership, and innovation. He has an unlimited tonnage USCG Third Assistant Engineer’s license for steam, diesel and gas turbine vessels. In 2014, Ross was honorably discharged from the US Navy Reserve as a Lieutenant after 9 years as a Strategic Sealift Officer. Prior to joining FMM, Ross was the VP of Technical Operations with Carnival Cruise Line.Executive Mentor

Francesco Greco, MSc, MA, P.Eng., PMP®
Marine Engineer
Francesco Greco, MSc, MA, P.Eng., PMP® is a Naval Architect and Marine Engineer currently working as the Fincantieri Marine Group Deputy Chief Operating officer in Washington D.C. Francesco obtained a Master of Science in Marine Engineering and Naval Architecture Degree from the University of Naples (Italy) where he applied CFD models to drag predictions of Small Water plane Area Twin Hulls. He also holds two M.A. degrees in the field of International Security Studies from the University of Venice (Italy) and from the University of Rome (Italy). He retired from the Navy as a Captain (O6) having served on multiple assignments both on the operational and technical organizations of the Italian Navy. He has also been the National Representative to NATO Naval Ship System Engineering and Mission Modularity Working Groups, as well as Capability Group for Naval Ship Design. He received his last PhD level diploma in Naval Vessels Design and Construction focusing on hydrodynamics as well as structural characteristics of warships from the Italian Navy School Command (Ancona) in Italy.Faculty Mentor
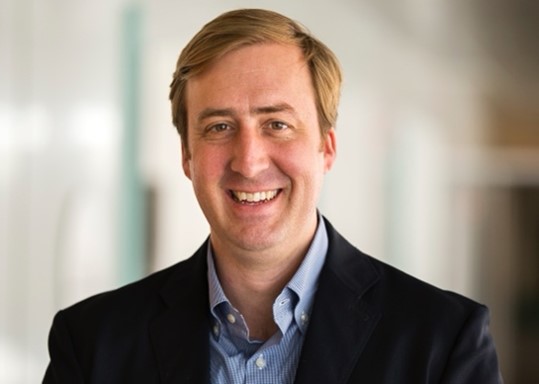
Kevin Maki
Aaron Friedman Marine Hydrodynamics Laboratory Director
Kevin Maki is a Professor and the Director of the Aaron Friedman Marine Hydrodynamics Laboratory in the Department of Naval Architecture and Marine Engineering (NA&ME). He received his Ph.D. from the NA&ME Department in 2006 and also has MSE degrees in Aerospace Engineering (2004) and NA&ME (2002). His research areas are in numerical and experimental naval hydrodynamics, hydroelasticity, and renewable energy related to the marine environment. He was a Summer Faculty Fellow in 2007 and 2009 at the Naval Surface Warfare Center Carderock Division, supported by the Office of Naval Research, and he has been a Visiting Professor at the Italian Ship Model Basin. He teaches courses on naval hydrodynamics and the design of sailing yachts and high-speed craft.Weekly Meetings: During the winter 2025 semester, the Fincantieri team will meet on Mondays from 3-5pm in 210 NA&ME.
Work Location: Most of the work will take place on campus in Ann Arbor, with at least one visit to the Fincantieri Marinette Marine shipyard in Marinette, WI to hold meetings with stakeholders, visit facilities, and give presentations. MDP will provide transportation.
Course Substitutions: CE MDE, ChE Elective, EE MDE, CoE Honors, MECHENG 450, MECHENG 490, MECHENG 590, NAME 499, NERS 499, SI Elective/Cognate
Citizenship Requirements: This project is open to US Citizens or Permanent Residents only due to the requirement to visit Fincantieri Marinette Marine.
IP/NDA: Student team members will sign IP/NDA documents that are unique to Fincantieri.
Summer Project Activities: No summer activity will take place on the project.
Learn more about the expectations for this type of MDP project