ASML manufactures complex lithography systems critical to the production of microchips, which use high-acceleration linear stages to accomplish incredibly precise tasks. Students on the ASML team will study the dynamics of rolling loops of wires and hoses on these systems, conducting research to develop a simulation of their dynamic behavior, and build a physical test rig to directly measure the resulting motion profiles.
Abstract:
ASML is an innovation leader in the semiconductor industry, manufacturing complex lithography systems critical to the production of microchips. This equipment uses high-acceleration linear stages to accomplish incredibly precise tasks. ASML builds linear stages with excellent bearings, including air bearings or magnetic levitation bearings, to achieve high precision motion control in challenging motion profiles. However, the electricity used by components on board the moving portion of the stage is brought in via stranded wires, called conductors. Additionally, depending on the type of stage, there may be air, vacuum, gas and/or water used onboard, which is brought by hoses. The conductors and the hoses comprise a rolling loop. This rolling loop adds dynamic complexity to the stage, since the effective moving mass and center of mass vary throughout the motion profile. This in turn affects the dynamics of the stage, and makes it more difficult to control with high precision. Students on the ASML team will study the dynamics of rolling loops, conducting research to develop a simulation of the dynamic behavior, and build a physical test rig to directly measure the resulting motion profiles.
Impact:
Since stages are controlled to maintain nanometer-level precision while moving at high speed and high acceleration, the dynamic behavior of rolling loops is very important to maintain the utmost precision.
Scope:
Minimum Viable Product Deliverable (Minimum level of success)
- Research and analyze the dynamics of rolling loops in linear stages, including methods for physical analysis
- Create a dynamic model of a simple linear stage, including the rolling loops
- Design and build a simple linear stage prototype, including the rolling loops, with the ability to minimally produce a simplified sinusoidal motion profile, and accommodate selected test rig measurement devices
Expected Final Deliverable (Expected level of success)
- Incorporate test rig measurement into the linear stage prototype to measure the dynamic behavior of the rolling loops. This should minimally include one of the following devices, or others not indicated:
- High speed cameras
- Strain gauges
- Load cells
- Perform low-speed measurements to validate physical test methods
- Process and report on methodology and data collected, and provide a final report
Stretch Goal Opportunities: (High level of success)
- Perform more realistic higher-speed measurements with several motion profiles
- Generate design guidelines for rolling loops, and include in final report
- Validate and update numerical model based on experimental findings
Mechanical Design and Prototyping (2-3 Students)
Specific Skills: Mechanical Design skills and knowledge. Techniques for fast prototyping.
Experimental Testing and Evaluation.
Likely Majors: ME, AERO, ISD-MFG
Mechanical Dynamics Modelling (2-3 Students)
Specific Skills: Kinematic model development and simulation. Strong design skills.
Experimental Testing and Evaluation.
Experience with or willingness to learn software tools such as MATLAB or LabView.
Likely Majors: ME, ROB, SPACE, ISD-AUTO, ISD-GAME, Any
Sensor Integration (1-2 Students)
Specific Skills: Incorporation of wide range of sensors into greater system.
Basic Knowledge of cameras, strain gauges, and load cells.
Likely Majors: EE, CE, ME
Additional Desired Skills/Knowledge/Experience
- Self-Drive
- Customer focus and requirements elicitation
- Demonstrated success in team-based technical work
- Communication skills and initiative to communicate
- Academic or work experience in design for manufacturability
- Experienced fast prototyping skills (3D print, CAD design)
- Strong interest in engineering design
- Interest/curiosity in starting a career in the semiconductor capital equipment industry
Sponsor Mentors
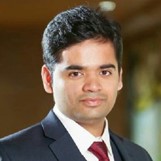
Siva Chillara
Siva has a PhD in Mechanical Engineering from The Ohio State University where he did research in morphing structures for the enhancement of aerodynamic performance of automobiles, sponsored by Toyota Technical Center (Ann Arbor, MI). He is currently a Lead Mechanical Architect at ASML, and has experience in mechanical architecture, development of new designs, and innovative upgrades to the reticle stage in the Deep Ultraviolet (DUV) lithography systems. Siva has also worked in the automotive industry, and was a founding member of the National Institute of Technology Karnataka FSAE team.
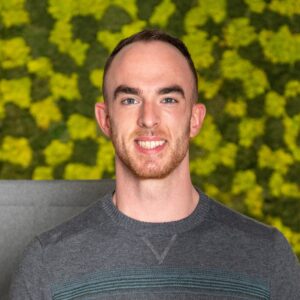
Matthew Sorna
Matthew has his BS in Engineering Science and Mechanics from Penn State University, ’17, and his MSE in Mechanical Engineering and Applied Mechanics from the University of Pennsylvania, ’18. He is a licensed Professional Engineer and has been with ASML since 2019 – primarily in his role as Analysis Architect in the Mechanical Development department. Matthew’s most recent work focuses primarily on development of reduced-order-models for large-scale system dynamics evaluations using FEA, as well as coupled flow-thermal CFD analyses to predict motor cooling performance in DUV lithography systems.
Executive Mentor
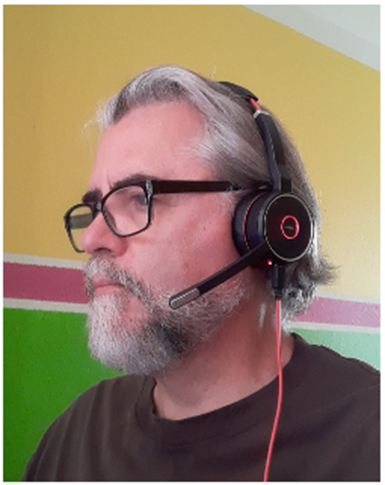
Santiago del Puerto
Santiago del Puerto has his BSME and MSME from Columbia University ’82 ‘83
He worked for IBM from 1983 – 1994 in Test Equipment Engineering (Wafer Final Test). He has worked at ASML since 1997 on multiple projects in Deep UV and Extreme UV lithography, mostly on scanning stages, especially lately.
He worked in a huge machine shop between ’94 and ’97, making just about anything imaginable, including setting up and wiring a new building for the shop to move to and expand, and managed to live through the construction without being buried alive, electrocuted, etc. He kept all fingers intact while later playing with the machine tools (I can tell some good stories about the building and the machining). This job was a lot of fun, but didn’t pay very well.
Hobbies: Bicycle designing, building and riding, propagating plants and trees. Juggling. Anything mechatronic-like encountered that needs improving, life-extending, cost-reducing or fixing. Presently engaged in a hobby project to create human-powered apparatus for swimmers that emulates marine mammals and/or fish.
Faculty Mentor
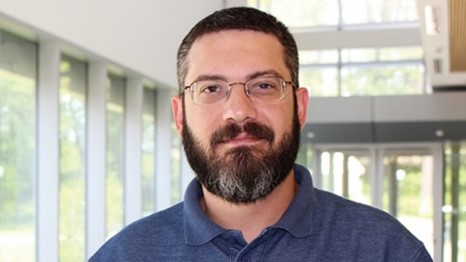
Robert Middleton
Assistant Research Scientist, Mechanical Engineering
Rob’s research interests include combustion, focusing primarily on automotive engines, simulations of spark ignited and advanced auto ignition combustion modes using 1D models and 3D CFD including large scale parallel simulations, and the impact of fuel properties and kinetics on engine efficiency and emissions. Rob is an experienced MDP mentor.
Work Location: Most of the work will take place on North campus in Ann Arbor.
Course Substitutions: CE MDE, ChE Elective, EE MDE, CoE Honors, MECHENG 490, MECHENG 590, ROB 490, SI Elective/Cognate
Citizenship Requirements: This project is open to all students. Note: International students on an F-1 visa will be required to declare part time CPT during Winter 2024 and Fall 2024 terms.
IP/NDA: Students will sign IP/NDA documents that are unique to ASML.
Summer Project Activities: No summer activity will take place on the project.
Learn more about the expectations for this type of MDP project